COMMON INSULATION MATERIALS
Let’s look at common insulation materials. What types of insulation are best? How to spec industrial insulation? When considering an insulation solution, you must first ask the question… “What is my application and condition?” The industry is smothered with options, but the real question one must ask is…” Which insulation option gives me the best result?” Mechanical systems are complex, they involve a bit of common sense, coupled with an in-depth product knowledge with proven results. So, what is your expectation on the finished result? It always reflects on life cycle cost, ROI, payback period, and measured performance. Are your expectations clear and do you see a need to return to the problem within a short timeline or is the expectation a one and done, forgotten solution, so you can move onto the next challenge and be rest assured, the insulation solution will perform for many years, problem free and highly effective? How to rank the the best industrial insulation solutions? Pros and Cons of various of types of insulation are listed below as a guide:
Here are some common approaches, with common insulation materials. Applying these materials under the correct conditions, will lead the investor (That is You) towards a path of a long-lasting solution and a sound investment for years to come. Best practices should consider thermal efficiency, durability, containment, access for maintenance and long-term wear and tear from physical exposure.
CONVENTIONAL INSULATION SOLUTIONS
With so many conventional insulation materials available, the user must select the best, most cost-effective solution. Consideration to material selection and jacketing will generate a good or great performance, long term. Again, like blanket insulation, there should be an expectation on long term performance.
COMMON INDUSTRIAL INSULATION MATERIALS:
Hydrophobic – CUI – Thermal Blanket Insulation | ||||||||
---|---|---|---|---|---|---|---|---|
Insulation Type | K Value | Density | Temp Range | Jacketing Required | Airborne Dust | Re-Usable | Attribute | Hydrophobic |
Blanket Insulation – EMat | 0.26 | 11 lb/ft3 | 1100F | Self Jacketed | No | Yes | Flexible | No |
Blanket Insulation – Ceramic Mat | 0.24 | 8 lb/ft3 | 2000F | Self Jacketed | No | Yes | Flexible | No |
Blanket Insulation – SuperMat® | 0.26 | 9 lb/ft3 | 600F | Self Jacketed | No | Yes | Flexible | Yes |
Fiberglass Pipe Covering | 0.23 | 3.25 lb/ft3 | 850F | Yes | No | No | Stiff | No |
Mineral Wool | 0.24-0.26 | 6-10 lb/ft3 | -20F to 1200F | Yes | Yes | No | Stiff | No |
Foamglas® Cellular Glass | 0.35 | 8.5 lb/ft3 | -450F to 900F | Yes | No | No | Stiff | Yes |
Elastomeric Foam | 0.28 | 4-8 lb/ft3 | -70F to 250F | No | No | No | Flexible | Yes |
Urethane | 0.14 | 1.6-2.1 lb/ft3 | -80F to 200F | Yes | No | No | Stiff | Yes |
Calcium Silicate | 0.38 | 13 lb/ft3 | 1700F | Yes | Yes | No | Stiff | No |
Protective Jacketing
Most important, insulation must be protected with an exterior jacketing, complimenting the service condition both exterior and interior to the insulation material applied. Common jacketing materials include Aluminum (Smooth, Embossed & Corrugated), Stainless Steel (Smooth, Embossed & Corrugated), Fabric (Canvass, ASJ), Pittwrap® (Bituminous Jacketing) and Plastic (PVC). Each material works well, specific to the condition.
FIBERGLASS PIPE COVERING / ASJ ALL SERVICE JACKETING
The most common of all conventional insulation materials, fiberglass and ASJ are integrally attached, making installation simple. The ASJ jacketing includes an adhesive, self-sealing flap or lip to assure easy installation. Applications are widespread for hot water, steam and some process systems. Materials are easy to cut and shape, specific to pipe and large diameter surfaces. ASJ jacketing is susceptible to water and vapor, since the jacketing material is porous and sensitive to elevated temperature. Consider this combination of materials for commercial and light commercial applications (Mechanical Rooms, Boiler Rooms). Fiberglass insulation is porous and is susceptible to water, moisture and wicking. Fiberglass Insulation is rigid however fiberglass, with a low compressive strength and weak structural integrity, it cannot withstand being walked on.
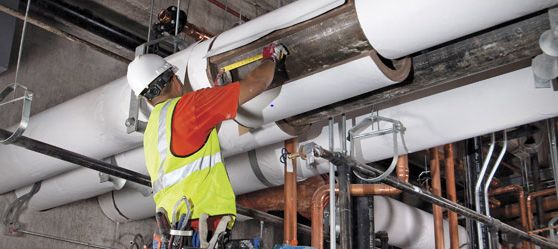
Pros:
- Easy to Install, minimum manhours
- Good Thermal Performance
- Readily Available
- Inexpensive
Cons:
- Must be kept DRY
- Not Weatherproof
- Easily Damaged
- Insulation filler is susceptible to crushing if walked on
- Not repairable
- Short service life
- Limited to round and flat surfaces
- Is NOT REUSABLE
Applications:
- Pipe
- Tank/Vessel Surfaces
FIBERGLASS PIPE COVERING / ALUMINUM JACKETING
Another common approach to insulating systems that require protective surfaces from exterior elements (Wind, Rain, Water). Fiberglass pipe covering is easy to install, featuring ASJ jacketing with a self-sealing adhesive strip overlap. Once installed, aluminum jacketing (0.016” thickness) is shaped and cut to match the pipe covering surface. The jacketing material is offered in a smooth surface, embossed surface and corrugated surface, each referenced to a specific condition or required finish. Aluminum jacketing offers an inner poly moisture retarder. The finished exterior surface is abrasion resistant. Materials are secured using metal screws. Once installed, the aluminum metal jacketing protects the fiberglass to assure proper thermal performance. Fiberglass insulation is porous and is susceptible to water, moisture and wicking. Fiberglass Insulation is rigid however fiberglass, with a low compressive strength and weak structural integrity, it cannot withstand being walked on.
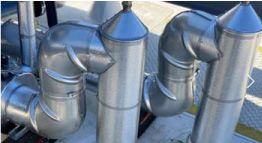
Pros:
- Good Thermal Performance
- Readily Available
- Inexpensive compared to stainless steel
- Weatherproof
Cons:
- Must be kept DRY
- Insulation filler is susceptible to crushing if walked on
- Not repairable, damaged metal is difficult to repair
- Longer service life, but dependent on insulation filler holding shape
- Limited to round and flat surfaces
- Is NOT REUSABLE
Applications:
- Pipe
- Tank/Vessel Surfaces
FIBERGLASS PIPE COVERING / STAINLESS STEEL JACKETING
Another common approach to insulating systems that require protective surfaces from exterior elements (Wind, Rain, Water, Acidic and Basic Conditions). Fiberglass pipe covering is easy to install, featuring ASJ jacketing with a self-sealing adhesive strip overlap. Once installed, stainless steel, type 304 & type 316 jacketing is shaped and cut to match the pipe covering surface. The jacketing material is offered in a smooth surface, embossed, and corrugated surface, each referenced to a specific condition or required finish. Stainless steel jacketing offers an inner poly moisture retarder. The finished exterior surface is abrasion resistant. Materials are secured using metal screws. Once installed, the stainless-steel metal jacketing protects the fiberglass to assure proper thermal performance. Fiberglass insulation, a common insulation material, is porous and is susceptible to water, moisture, and wicking. Fiberglass Insulation is rigid however fiberglass, with a low compressive strength and weak structural integrity, it cannot withstand being walked on.
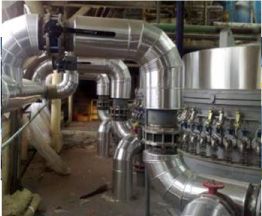
Pros:
- Good Thermal Performance
- Readily Available
- Fiberglass pipe covering is inexpensive
- Weatherproof
Cons:
- Must be kept DRY
- Insulation filler is susceptible to crushing if walked on
- Stainless steel jacketing is expensive
- Not repairable, damaged metal is difficult to repair
- Longer service life, but dependent on insulation filler holding shape
- Limited to round and flat surfaces
- Is NOT REUSABLE
Applications:
- Pipe
- Tank/Vessel Surfaces
MINERAL WOOL
Popular in Canada and Europe, a cost-effective insulation material with a wide service temperature. Mineral wool is a spun fiber derived from inorganic, basalt volcanic rock, combined with a thermosetting resin, to suspend the fiber and produce a geometric shape. Mineral wool insulation can be combined in a similar fashion with aluminum, PVC and stainless-steel protective jacketing. Mineral wool insulation is offered without any exterior jacketing (ASJ or otherwise) to assist in holding a uniform shape, so an exterior jacketing is absolutely necessary. Although a common insulation material, mineral wool insulation is porous and is susceptible to water, moisture, and wicking. Mineral wool is rigid however mineral cannot withstand being walked on, with a low compressive strength.
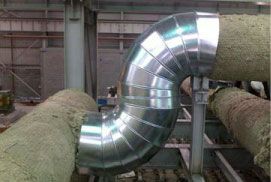
Pros:
- Good Thermal Performance
- Readily Available
- Easy to cut and shape in the field
- Inexpensive
Cons:
- Must be kept DRY
- Not weatherproof without jacketing
- Insulation filler is susceptible to crushing if walked on
- Jacketing required (Aluminum, Stainless, PVC)
- Not repairable
- Limited to round and flat surfaces
- Is NOT REUSABLE
Applications:
- Pipe
- Tank/Vessel Surfaces
FOAMGLAS® CELLULAR GLASS INSULATION
A rigid, lightweight, closed cell insulation, created from heating glass particulate to extreme melting temperatures. With a blowing agent (carbon or limestone) the granular glass expands and foams, producing gas pockets. Highly chemical resistant, cellular glass can be shaped and ground into curved side wall segments, pipe covering and flat block. Incorporating an exterior jacketing (Aluminum, Stainless Steel, PVC or Pittwrap® Bituminous Jacketing), Foamglas® cellular glass is ideal for complex insulation environments. Extremely rigid, Foamglas® is susceptible to thermal cracking, so the outer jacketing component is critical in its success.
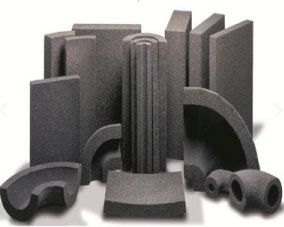
Pros:
- Good Thermal Performance
- Readily Available
- Easy to cut and shape in the field
- Inexpensive
Cons:
- Not weatherproof without jacketing
- Insulation filler is susceptible to crushing if walked on
- Susceptible to thermal cracking
- Jacketing required (Aluminum, Stainless, PVC)
- Not repairable
- Limited to round and flat surfaces
- Is NOT REUSABLE
Applications:
- Pipe
- Tank/Vessel Surfaces
ELASTOMERIC FOAM
Elastomeric EPDM insulation material is ideal for HVAC applications, involving surface conditions below ambient temperature. Any surface requiring a closed cell insulation, where condensation of water droplets form as a result of below temperature surface conditions. Ideal for chilled water (45F-60F) elastomeric form is pliable and flexible, easy to cut and shape and easy to install. A self-adhesive version bonds well to surfaces to achieve a full encapsulation of insulated surface. Elastomeric form insulation is favored over typical fiber insulation when applying materials in air sensitive environments.
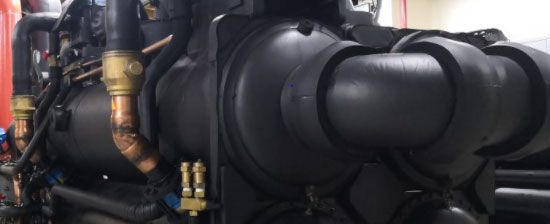
Pros:
- Good Thermal Performance
- Readily Available
- Easy to cut and shape in the field
- Repairable
- Available with zero-perm laminated aluminum facing
- Can be expensive with facing option
Cons:
- Difficult to jacket (typically left unjacketed)
- Exterior surface is susceptible to tearing
- Limited to round and flat surfaces
- Is NOT REUSABLE
- Difficult to remove, for inspection and or repair
- Temperature limit of 250F
Applications:
- Pipe
- Ducting
- Tank/Vessel Surfaces
- Liquid Chillers
- Chiller Water Pumps
- Heat Exchangers
- Water Boxes
URETHANE
Urethane (Polyisocyanurate) is a rigid, foam insulation fabricated into board, pipe, and curve side wall segments. A great insulation value, applied correctly, urethane insulation is a closed cell insulation with a temperature limit of 200F. Ideal for cold surface conditions up to -80F, field installation is easy but messy (dusty). Urethane insulation is water resistant and mold resistant. Being dense and rigid with a high compressive strength, urethane insulation, coupled with a jacketing/facing material is highly durable.

Pros:
- Great Thermal Performance
- Readily Available
- Easy to cut and shape in the field
- Not Repairable
- Available with optional facings
Cons:
- Difficult to install when applying an external jacketing
- Limited to round, flat and simple geometric surfaces
- Is NOT REUSABLE
- Difficult to remove, for inspection and or repair
- Temperature limit of 200F
Applications:
- Walls
- Ceilings
- Pipe
- Ducting
- Tank/Vessel Surfaces
CALCIUM SILICATE
Calcium Silicate Insulation (Ca2SiO4) is a proven traditional, high temperature insulation material used in all insulation markets and applications requiring a robust, durable insulation system that stands the test of time, in the most complex, difficult environments. It is derived from limestone and diatomaceous earth, both natural materials, with a high service temperature (1700F) and very high density (181 lb/ft3). Balancing insulation performance with durability, Calcium Silicate is used in the power generation and process markets because of its robust characteristics. Field fabrication, shaping and molding to field conditions is labor intensive, along with the necessary metal jacketing requirement, field labor cost is much higher than fiber-based insulation materials. Once installed and jacketed, calcium silicate insulation historically performs at a high level, with a problem free service life. Complimentary jacketing materials include aluminum, stainless steel and PVC. Calcium Silicate Insulation MUST include a jacketing material because the insulation is easily damaged by water penetration, moisture, and weather.

Pros:
- Good Thermal Performance
- Great Durability Long Term
- High Density (Can Be Walked On)
- Available with optional Aluminum, Stainless or PVC jacketing
- Temperature limit of 1700F
Cons:
- Must be kept DRY
- Difficult to field repair
- Difficult to install when applying an external jacketing
- Difficult to cut and shape in the field
- Creates a lot of airborne dust during field cutting and fabrication (Face Masks Required)
- Limited to round, flat and simple geometric surfaces
- Is NOT REUSABLE
- Difficult to remove, for inspection and or repair
Applications:
- Pipe
- Tanks
- Vessels
CONVENTIONAL INSULATION VS REUSABLE BLANKET INSULATION
- Conventional Insulation is applied.
- Insulation is removed (Inspection, Service, Repair)
- Insulation is never “Re-Installed”.
- Flanged Fittings, Complex Surfaces remain untreated.
- The result is a large radiant surface area.
- The result is WASTED ENERGY !
- Most WASTED ENERGY is fittings, not pipe.
- Gate Valves, Control Valves, Strainers, Flanges, Pumps, Equipment (Complex Geometry)
REMOVABLE / REUSABLE BLANKET INSULATION
Reusable blanket systems vary in jacketing and insulation materials, depending on the service application. Integral fasteners allow easy removal and re-installation, ID Tagging assures location identification. The design approach is to create a high-quality geometry to assure re-installation. If designed and manufactured correct, you can expect a 15 year service life. Again, consider blanket insulation on all complex surfaces which require easy access for service, inspection and or repair. Temperature limits range from slightly below ambient (45F) to 2000F. Remove and re-install just one time and the economics of a reusable blanket will far outweigh a conventional insulation approach. Select the “Correct” blanket design for the application, this is the key to success. On average, a fitting cost is $300, with a $150-$200 annual savings in energy. If the design is correct, the expectation is 15 years of performance, savings ($150 x 15 = $2,250 or $200 x 15 = $3000), per fitting!
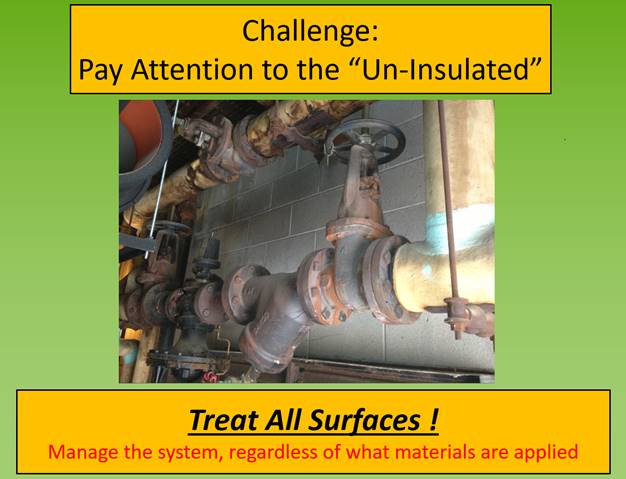
SELECTING THE CORRECT BLANKET DESIGN:
Pros:
- Very Low installation cost
- Easy to remove and re-install, within minutes
- Easy access for inspection, service and repair
- Good Thermal Performance (Hydrophobic Option)
- Resists Carbonic Acid (Acidic & Basic Field Conditions)
- Blanket designs match the field and service conditions (to assure a 15-year service life)
- Blankets are designed to match complex surfaces
- Insulates the surfaces that are left untreated from conventional insulation
- Blankets are repairable / replaceable
- IS TRULY REUSABLE and REMOVABLE
Cons:
- Not water tight, not a sealed system
- High material cost
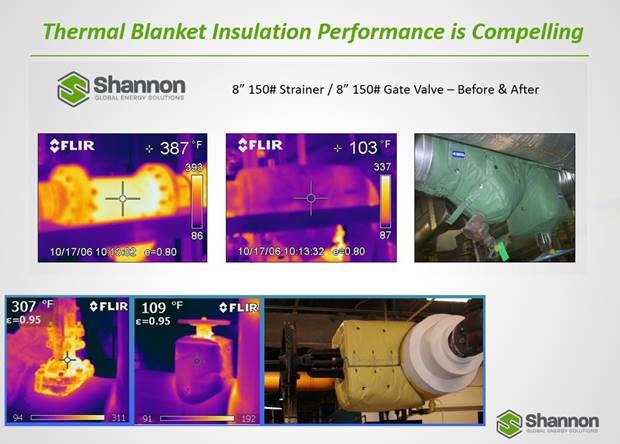
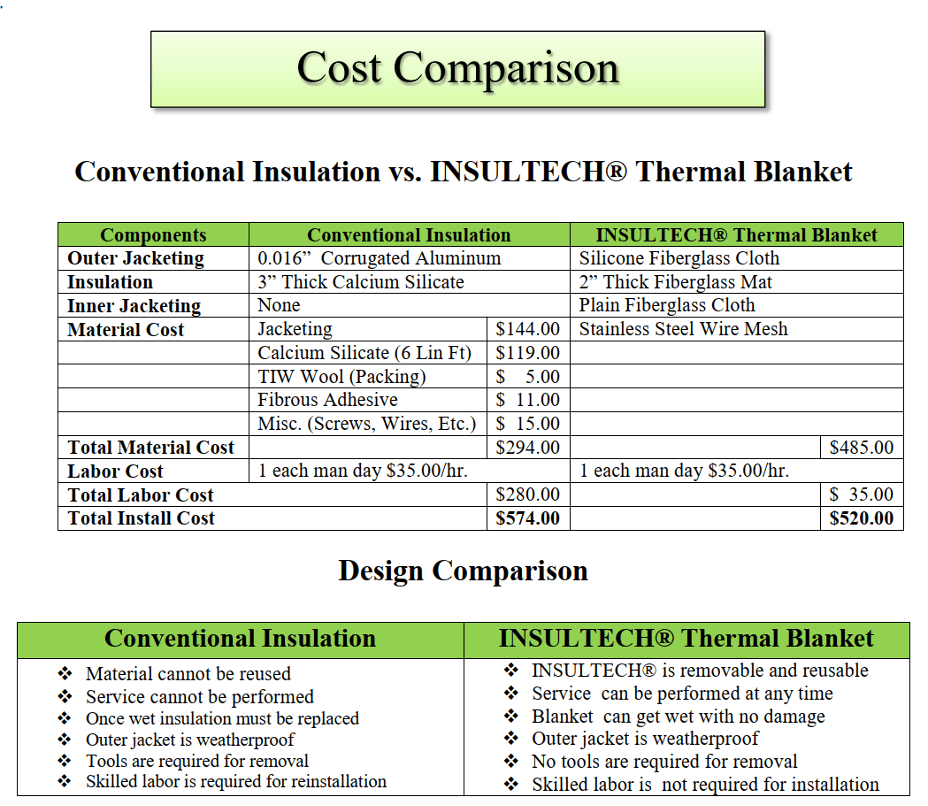
IN CONCLUSION
There are solutions to each condition (Process Systems, Outdoors, Accessibility, Hydrophobic, Chemical Environment, Temperature, Complex Surfaces…Etc). You must do your research and make your decision based on the facts. Traditional insulation approaches are a safe avenue to problem solving however, consider the new technologies that could radically improve life cycle cost and performance on the system design.
Keep in mind, that all insulation is removable. If it gets removed, then there must be considerations to allow removability without disrupting the conventional materials in place. Each common insulation material has its pros & cons, so consider all options. Ultimately, there are industry standard guidelines (ASTM Testing, CSI-Construction Specifications Institute, 3 Part & 10 Part Spec Standards, Master Spec, National Insulation Association) to guide your decision.
Treat your decision as a capital investment with a performance measure with given expectations. Done properly, you will see a long-term benefit with minimal disruption, high ROI and limited risk.