Extensive Energy Use
Hospitals tend to have a high Energy Use Intensity (EUI) compared to other building types, nearly three times the average commercial building¹. They are currently the second most energy-intensive building type in the U.S., with heating, cooling, and ventilation (HVAC) comprising 52% of their energy use².
Hospital Steam Systems are Vital
Hospitals rely on steam boiler systems for various purposes, such as heating, humidification, and sterilization. Here are some of the main applications of boilers in hospitals and why they are indispensable:
HEATING
One of the primary functions of a steam system is to provide heat to the whole building. This is especially important for hospitals, where patients and staff need to be comfortable and safe at all times. A general guideline is between 20°C and 24°C (70° to 75°F). Cooler temperatures help keep bacteria growth at a minimum. A steam boiler system can efficiently distribute heat throughout the facility, even across multiple floors. A boiler system is also more economical than other heating options, as it can adjust its output according to the demand.
HUMIDIFICATION
Another vital role of a steam boiler system is to maintain the optimal level of humidity in the hospital environment. The relative humidity inside a hospital should be between 30% and 60% depending on the specific requirements. This is because certain pathogens, such as viruses, bacteria, and mold, can thrive in either too dry or too moist conditions. A boiler system can help prevent the spread of these harmful agents by producing steam that regulates the humidity in the air. This way, the hospital can provide a safe and healthy atmosphere for both patients and staff.
STERILIZATION
A third essential use of steam boilers in hospitals is to sterilize medical equipment, tools, and instruments. These items need to be free of any germs or contaminants. Of all the methods available for sterilization, moist heat in the form of dry saturated steam under pressure is the most widely used and the most dependable. Steam sterilization is nontoxic, inexpensive, rapidly microbicidal, sporicidal, and rapidly heats and penetrates fabrics. A boiler system can help achieve this by generating steam that reaches high temperatures and pressures, killing any microorganisms that may be present. To perform steam sterilization, four factors are important: steam quality, pressure, temperature, and time. The steam should be dry / saturated, and the pressure should be high enough to reach the desired temperature. The most common temperatures are 121°C (250°F) and 132°C (270°F), and the exposure time depends on the type of item and the sterilizer. Steam heat is often a safer way to sterilize than using potentially harmful chemical agents. A boiler system can also supply steam to autoclaves that use steam to sterilize medical waste and other materials.
FOOD SERVICES
A fourth area of the hospital that relies heavily on the boiler system is the kitchen. The kitchen staff has to prepare and serve meals for hundreds or thousands of people every day, including patients, staff, and visitors. This requires a lot of hot water for cooking, cleaning, and sanitizing the food and utensils. The boiler system provides the hot water and steam needed for these tasks, as well as for heating the kitchen space. Without a reliable and efficient boiler system, the hospital kitchen would not be able to function properly.
LAUNDRY SERVICES
One of the hidden but essential aspects of hospital operations is the laundry room. Every day, hospitals generate tons of dirty linen that need to be washed, dried, and sanitized. This includes patient gowns, bed sheets, blankets, towels, and more. To ensure that the laundry process meets the high standards of hygiene and infection control, hospitals need to use hot water and steam in large quantities. That’s why many hospitals have a dedicated boiler system for their laundry room, separate from the main steam plant that serves other purposes. The laundry boiler system is responsible for producing enough steam to heat the water used in the washing machines and dryers.
How to Save Energy in Hospital Steam Systems
Healthcare Facilities Managers, Sustainability Directors and ESG Officers are always looking for ways to reduce energy in their facilities. As this article highlights, steam systems are essential for hospitals and healthcare facilities to function. The good news is you can save energy, reduce costs, and reduce emissions by minimizing radiant heat loss to improve efficiency. Whether you are maintaining a current system or considering installing new equipment, mitigating radiant heat loss is crucial for optimization.
RADIANT HEAT
Thermal Radiation is a process by which energy is emitted by a heated surface in all directions and travels to its point of absorption. Ideally you want your energy kept within the system until the point of use is reached.
With Steam System Piping, Fittings, Valves, Flanges, Pumps, Strainers, Steam Traps, the steam passing through the system will conduct heat to the piping and other equipment and, if unchecked, will radiate heat energy as waste long before it gets to its usage point — diminishing the usable energy for its intended purpose.
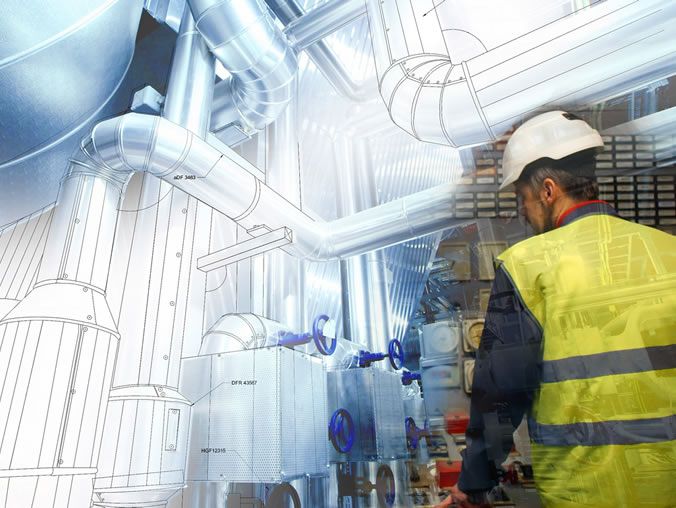
SURFACE AREA
It is a standard practice to insulate Steam Piping to reduce radiant heat loss. A conventional hard insulation is used for this purpose. The most common of all conventional insulation materials, fiberglass and ASJ are integrally attached, making installation simple. Applications are widespread for hot water, steam and some process systems. Materials are easy to cut and shape, specific to pipe and large diameter surfaces. It is not reusable. Long runs of consistently-shaped Piping with standard diameters are insulated this way.
Now, think about Valves, Flanges, Steam Traps and other fittings and equipment with complex surfaces. Because of their complexity and need for accessibility, they are often left uninsulated. Components needing regular inspection and maintenance require a removable and reusable insulation solution. Thermal insulation blanket systems, correctly sized and engineered for the particular component and application are removable and reusable. With integral fasteners and proper fit, insulation blankets are easy to install, remove for access and then easily reinstalled by maintenance staff.
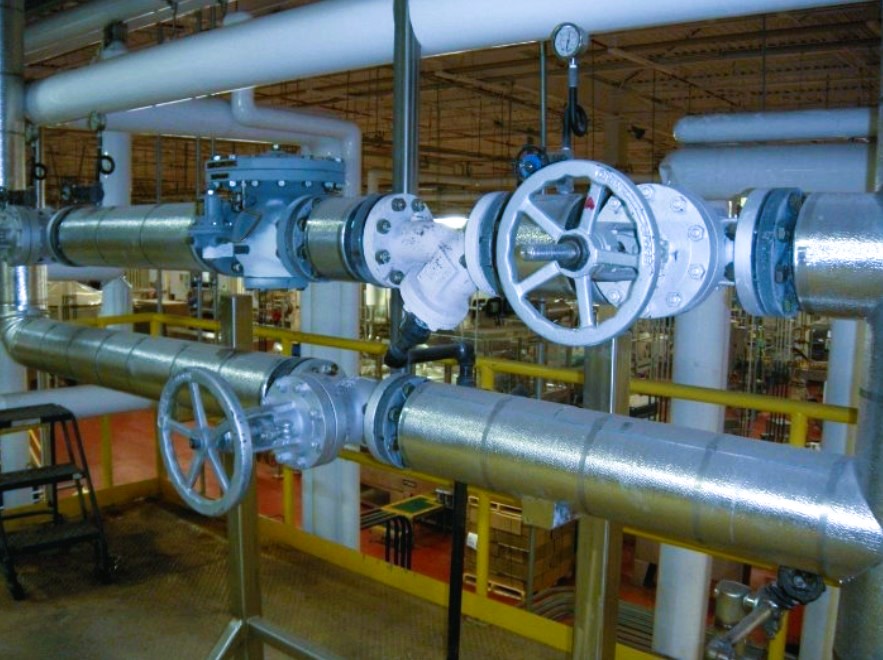
Does it make a difference? Yes. These Valves and fittings may look like a very small part of a large piping system, but because of their geometric complexity they have a lot of surface area. More surface area creates more opportunity for heat loss. How much? As an example, Four 10-inch 150# gate valves will have the equivalent surface area to nearly 20 feet of 10-inch pipe. A typical Hospital steam system has over 500 fittings!
LOCATE THE SOURCES OF RADIANT HEAT LOSS
A Shannon Energy Survey can show you, systematically, the areas where you are losing significant radiant heat in your steam system. View this video for examples. In the average Healthcare Facility, mitigating radiant heat loss in steam systems provides savings that are substantial and ongoing.
REVIEW THE SUPPORTING DATA
At Shannon, we have helped hospitals and healthcare facilities achieve their goals in energy efficiency, cost reduction and emissions reduction with high quality engineered thermal blanket insulation systems that are removable and reusable. Contact us for information about our energy conservation measures, supporting data, payback periods & ROI, and hospital client case studies.

¹Della Barba, M.P. (2014). Optimizing Energy Use in a HealthCare Setting. 22nd National Conference on Building Commissioning.
²Taylor, S. and M. Arch. (2016). Breathe easy: Two basic steps to improve patient outcomes and healthcare reimbursement.
https://www.energy.gov/femp/articles/integrating-health-and-energy-efficiency-healthcare-facilities
